It’s really important for a Supplier Quality Management Program to work effectively with an auditing mechanism if one is to maintain Quality Compliance.
One way to achieve this is to school one’s suppliers to operate as close as possible to your methodology in order to reduce risk.
Today risk management is extremely important and part of expectations promulgated by the FDA, so it’s very important to incorporate a Risk Management component into any Forward Strategy for Operational Quality. In building this type of approach then, it is very important to know and understand the prevailing Regulatory Landscape and risk factors associated with your system, including any that may require a degree of mitigation.
For FDA compliance this should always be measured against documents like ICH Q9 (International Conference on Harmonization), to assure that key points are not overlooked or missed altogether.
As a rule, core risk management features that should be addressed include:
1. Those types of proactive measures that assess the probability and potential consequences of certain actions.
2. Preventive actions and measures that reduce the probability of negative outcomes.
3. Implementation of tools to predict or anticipate potential problems and issues.
4. If problems do arise, then swift implementation of pre-determined measures to minimize negative outcomes.
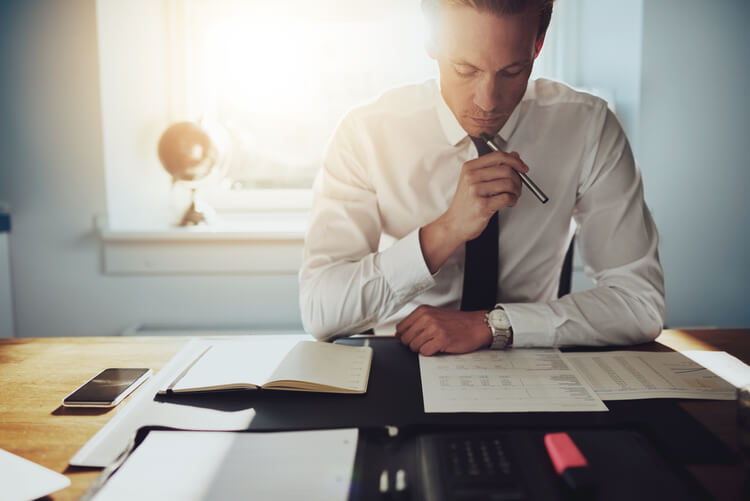
Some other important features that can be covered through the use of a good pre-screening questionnaire include such things as:
1. The financial stability of the company
2. The existence of a suitable cGMP culture within the company that embraces appropriate regulations and guidance’s, such as FDA and ICH documents covering regulations and guidance.
3. Existence and implementation of an internal Quality System
4. Existence of an exemplary regulatory compliance record with the key Regulatory Agencies.
5. A strong technical and management presence that understands the requirements of the Life Sciences business.
6. A satisfactory delivery performance record, on-time and specification.
7. Appropriate capacity to meet the needs of your demands both now and in the future.
8. A strong production controls culture, together with a trouble free environmental record.
Important in the satisfactory use of this questionnaire tool is the need to make it as clear as possible to ensure that the most relevant information is communicated. Being patient to build this tool then is a great investment in one’s time and energy, so the more comprehensive that this is made, the greater the eventual return on investment will be.
In terms of socio-management connectivity, it’s vital for a successful client-supplier relationship that there be strong supplier management personnel capabilities blended with great group chemistry and cultural fit in order to enable the fostering of a trouble free long-term relationship.
The Key point to keep in mind as one goes through this exercise is that the objective is to maintain the risk associated with the use of the supplier’s material as low as possible and this is best achieved by clearly understanding those factors which are introducing the risk into the equation.
In building a compliant Supplier System it’s important to recognize those things that drive that process forward.
Certainly, an effective internal management structure is a foundational component upon which the roles of the individual players needs are clearly delineated.
The mechanism of how to conduct the audit should also be clearly and widely understood, as should what the audit report should contain and how it should be reported.
In selecting a team to conduct this function, its important to structure the management of the activity as a cross-functional responsibility, with inputs from a variety of departments such as Technical Manufacturing Operations, Quality, Purchasing and, Materials Management.
The goal is to develop a supply network that can support your manufacturing operations for both the current capacity and the projected future market. In addressing this need, one provides the best possibility to guarantee a robust supply system free of issues and this provides you with an acceptable quality outcome.
As a contributory feature to managing this process, it is best to designate a primary point of communication with the supplier and to assure that all contact goes trough that person to avoid confusion and the transmittance of misinformation.
Even if technical communications are needed between both sides, it’s still advisable to arrange a linkup between the points of contact first, where ground rules are established, before involving face to face discussions between the respective technical specialists. In this way a smooth level of communication is established and potential for difficulties is avoided.
As a good management methodology, these meetings should all be recorded through the dissemination of written minutes to avoid the potential for confusion.
As a rule, all key aspects of the supplier agreement should be covered in a Quality Agreement signed by both parties and this should cover all specification and technical aspects and expectations.
Any changes to this Quality Agreement should be formally managed by a Change Control Process and this should be covered with the agreement of the client company and this should be documented.
Separately the business details should be specified in a sister business agreement.
In cases where the supplier cannot agree with the wishes and/ or expectations of the client company, there needs to be the provision of an escalation process that will involve representatives of each organizations’ senior management.
This should be a mechanism that seeks conciliation and a route to an acceptable solution to overcome the difficulties raised at the supplier relationship management level.
Complementary to this however, the client company must have a mechanism to disqualify the supplier should their performance not met the agreed upon standards outlined in the Quality and Business agreements.
Performance of the supplier is maintained through an audit process that meets the requirements of the prevailing regulatory authorities in terms of rigor and frequency.
For FDA compliance, the client lead auditor should be sending a request letter to the supplier identifying the scope, duration and standards that will apply to the audit.
Internally, through the use of performance score cards, the client company should be determining if an audit is required, provided it is within the regulatory frequency period. This is usually two years for “Qualified” status for US FDA requirements.
Depending upon the requirements, the audit team will develop their checklist of issues and topics to be covered and this will be used as a primary tool to track the results of the audit process.
During the audit the auditor(s) will cover a review of the suppliers’:
1. Organizational Structure
2. Background information about the site
3. Past regulatory agency reports/citations
4. Their SOPs and other key documents such as manufacturing records, testing results, training records and validation records.
5. Deviation/non-conformance lists, together with investigations performed.
6. Job descriptions and resumes of staff.
Key for the audit is the facility tour, which will start and involve: the receiving /dispatch area, the warehouse, the process areas, the staging areas, the laboratory testing areas and the document control function.
The inspection is always started at the loading dock where an inspection of the material arriving is checked against the various requisitions and accompanying packaging documents. A review of how this is logged into the supplier system is always a good exercise at it demonstrates the robustness of the level of control.
Next, checking the sampling procedure for ID (Identity),and witnessing how material is sampled provides a good check that the content uniformity can be relied upon.
Watching also allows the auditor to see whether the supplier uses disposable utensils or stainless steel utensils and whether they have cleaning procedures in the case of the later.
Checking the tracking system into the warehouse is also a key activity at this point, as is checking how material is removed from containers and reconciled.
A review of the quarantine procedure is also valuable as is the procedure for the disposal of rejected material. Important is who can access such areas and what the level of security operated is the norm.
Checking the warehouse for monitoring systems for temperature and humidity should also be a priority, together with checking where raw material that requires refrigeration is kept. Assuring these are appropriately validated is a must and a review of the calibration and maintenance records should always be part of this process.
Checking how the material is removed to the manufacturing area should be a key point of note and how everything is labelled with weights, dates etc.
These should be clearly visible, not temporary paper attachments and in such condition as not to detach themselves as the material is moved.
In the process area its important to observe how the material is used and documented in the material records section of the manufacturing batch record.
Assuring that the equipment is properly cleaned, calibrated and set up for use in the cGMP room will be important to maintain cGMP compliance requirements. All documents pertaining to this will also need to be checked as complete with filled in data and appropriately dated signatures or operator initials.
Assuring the rooms have been appropriately cleaned is another complementary function that must be performed and their needs to be evidence of records which document cleaning and functional use.
Once the manufacturing process is complete, it is important to assure that the material is appropriately labeled and moved to a quarantined area of the warehouse complete with an appropriate bar coding mechanism designating its storage position.
With this complete, a tour of the laboratories and their systems is appropriate to be able to assure the material is of the correct specification as noted in the quality documentation.
Important here is to check in to see how the samples are logged in and processed, how the data is handled and how the reports are prepared. Supporting reagents, solutions and buffers are all carefully noted to assure standards and reference ranges are met. All data records are reviewed for evidence that data has been second person checked and whether the data loaded onto the LIMS system is authentic. Connected with this is the review of systems that are connected or are interfacing with the LIMs and whether sufficient safeguards such as password security systems are in place and adequate.
With the completion of the facilities tour, the key focus now is on a comprehensive review of the Quality documentation, so as to assure that it meets and supports the requirements necessary for cGMP production.
Key reviews will include but will not be limited to:
With the completion of the facilities tour, the key focus now is on a comprehensive review of the Quality documentation, so as to assure that it meets and supports the requirements necessary for cGMP production.
Key reviews will include but will not be limited to:
1. Change management
2. Training
3. Validation
4. Complaints
5. Deviations/investigations
6. Out of specification/Out of Trend
7. Corrective Action, Preventive Action
8. Manufacturing Controls
9. Laboratory Controls
10. Warehouse management
11. Batch Release
12. Audis
13. Stability management
14. Quality plan/management
15. Environmental controls
16. Cleaning
17. Calibrations and Maintenance
18. Quality agreements.
In each case the review needs to include a comparison of the written procedure against the actual practice, and observations will be noted where this deviates.
With the audit complete its important to record the “findings” in a suitable report and to inform the supplier’s staff verbally of the outcomes. This verbal feedback needs to be brief and to give the supplier company a head up as to the things you may not be completely happy with. This allows them to be proactive in correcting those, something most companies like to do where they may affect the business at hand.
The written feedback should be made available to the supplier’s audit interface within ten business days, with an expectation that any deficiencies will be addressed in a timely manner. Although not a requirement, it is usual that companies may discuss appropriate corrective actions together prior to receiving the audit report. This is a favorable approach because it helps to promote good inter company cooperation and a willingness by the client company to move suppliers towards “Qualified Supplier Status”, something that is desirable to both organizations since it promotes a Lean operation.