Over the last ten years we’ve seen a massive change in the way we look to manufacture biopharmaceutical products. Increasingly the methods and technology that were in vogue through the late 1980’s and 90’s are being superseded by new disposable options.
There are several reasons for this including, but not limited to:
Better products and more adaptable materials of construction, lower upfront costs for facilities and equipment, the potential for greater flexibility of production (particularly for clinical trial material), lower financial barriers to entry for early phase companies that have limited capital and easy scalability for low volume products that are now available from high producing cell lines.
When one looks deeper into the interface between upstream and downstream processing, the opportunity for tighter integration is available and this cuts down waste due to non-added value holding periods, cleaning time and chromatography column regeneration time.
The potential for upfront lead time reduction is also a significant advantage that disposable solutions offer as well as the opportunity to eliminate process time associated with process cleaning and re-sterilization.
For multiple low volume products manufacturing, whether it’s associated with either clinical or commercial manufacturing, disposables offer the advantage of more rapid change-over and this is another area which provides the opportunity to develop a lean manufacturing strategy.
However, the story is not all rosy as there can be problems associated with operational implementation.
To help address this the assistance of a pharmaceutical consultant is often needed to provide good advice and support when developing a robust strategy for the lean manufacturing/biomanufacturing of your biopharmaceuticals.
If you like this blog, let us know.
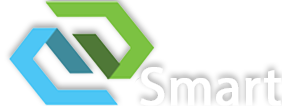
- Home
- Keynote Speaker
- About
- Services
- Resources
- Media And Publications
- Presentations
- Warning Letters, Consent Decrees and cGMP Compliance
- LEAN Laboratory Design and Process Operations in the QC environment
- Value Stream Mapping for Manufacturing Organizations
- Biopharmaceutical Processes: Waste
- Global Conference Presentation
- GxP Audit & Risk Management Presentation
- Achieving LEAN Process Implementation through Disposable Technology
- Aligning Quality Management Processes to Compliance Goals
- Achieving LEAN Processing through Disposable Technology and Systems
- Webinars
- Brochures
- FDA Resources
- Career Opportunities
- Contact
- Archives
Select Page